Deep-dive Into Service Network Management
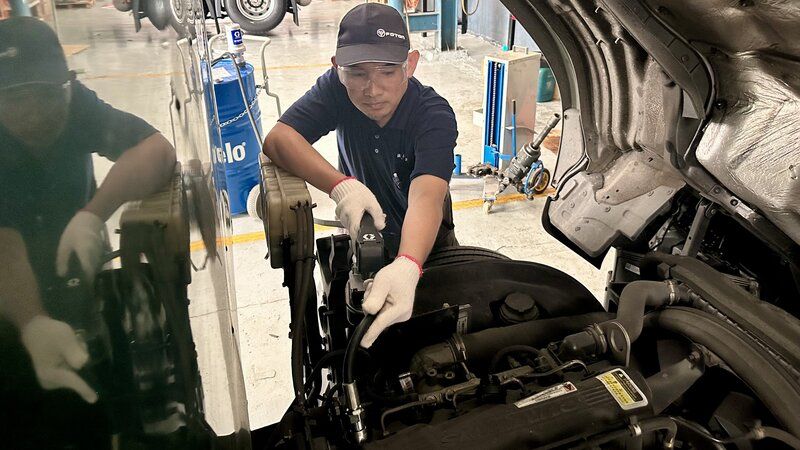
Asian Trucker takes a closer look at what it takes to provide a proper and professional service network that keep the trucks on the road, competitive charges and everyone safe and the driver happy.
A lot of the discussions revolving around trucks operators are not only on the purchase price but the following aftersales service and maintenance contracts, rescue services and predictive maintenance. These being hot topics, it is clear that the service network, the workshops operated by a franchised brand, is vital for the sustained success of any OEM brand. The success of the OEM/brands in supporting their customers operation is highly dependent on the way these workshops network operates. In this exclusive, Mr Tan Keng Meng, CEO of Warisan TC Holdings Bhd, offers insights into this topic. Considering that this discussion took place at C-Level is an indication as to just how important this subject is.
Why Workshops?
First of all, one would have to ask why any brand would need workshops at all. The answer is: for Aftersales support. What is important to point out immediately is that not all workshops are the same. The proper workshop should be authorised and certified, as Tan points out. “Workshops are part of a large ecosystem. They allow for the duties of the aftersales team to be performed.” Generally speaking, the scope of work divides into service, maintenance and repair. According to Tan, the task of the aftersales is to ensure that any truck would run in a safe and optimised manner, with an emphasis on the safety of the vehicle. The moment any vehicle is being put on the road, the need for service and maintenance arises, even if it is a brand-new truck.
A major difference between passenger cars and commercial vehicles is the usage: commercial vehicles clock in much higher mileage in shorter time than passenger cars as they are used to generate income. Angka-Tan Motor, as part of the Tan Chong Group, has more than 45 years of experience and an extensive service network. “This is important for our customers using Foton trucks. With over 40 service points, we offer convenience to them,” he explained. For Commercial vehicles with the increased wear and tear as a result of high usage, they need workshops to ensure regular services to keep the vehicle uptime and in safe and functioning.
Certified Competence
Trucks differ significantly in terms of technology used. On one hand that requires technicians to be highly trained on the vehicles of the brand they work on and on the other hand, it is maybe difficult for technicians familiar with one brand to work on another. Tan mentioned that this is why customers should insist on having trained, certified and qualified staff to work on their vehicles. The best way to ensure this that customers get the best service is by steering to the brand’s own service network rather than any third-party workshops. The latter may not only lack the expertise, but also the special tools and diagnostic software to perform the work. Technical expertise means that technicians are able to accurately diagnose any issues and provide the required remedy for any problem.
Whenever a new truck model is introduced (in Malaysia), technicians will need to be trained on the processes of service, repair and maintenance of the vehicle. To do so, the manufacturers/brand owners will train and evaluate the staff on their competence; this is one of the prerequisites for a workshop to be certified. The knowledge and adherence to the prescribed processes will be audited on a regular basis with re-fresher course being administered should the need arise. In the case of authorised workshops, Angka-Tan Motor would train and audit these third-party service providers in accordance with the knowledge the principal has imparted.
In addition to the availability of specialized original tools and diagnostic equipment, and the process know-how that is important, but the availability of genuine spare parts. These are, as per Tan’s elaboration, designed to run optimally as per OEM designed thereby ensuring safety, durability and reliability. A third party non genuine aftermarket parts may not be able to match the genuine parts. It may even affect the warranty terms.
Being genuine extends into the processes of how any vehicle is serviced, maintained or repaired, as stipulated by the manufacturer/brand owner. This is a compliance issue whereby the execution of any work in adherence to the original equipment manufacturer’s specifications ensures that the warranty is kept intact, and the vehicle’s components work in perfect harmony. “This is, why I don’t believe all workshops are created equally.”
At the same time ATM workshops offer fleet owner the service of their Fleet Management Program. “We offer this service to allow customers to maximize their investment in their trucks.” Within this ecosystem, the Foton Care, the TC Trust programme, is a comprehensive package to assist fleet owners to conduct their regular services. Tan urges fleet owners to adhere to the schedule as this will prevent any issues
that could arise when service is lapsed. It is of utmost importance to have wear and tear parts replaced as soon as it is deemed necessary.
Procedures to Perfection
At the heart of the operation are stringent standard operating procedures. Whenever a truck is being sent to the workshop, an initial, thorough inspection is conducted. A job card is being created, detailing the
work steps that are to be carried out, parts to be replaced and issues to the fixed. “In this context, this is extremely important. All these valuable data that we collect, will be used in many different ways. One important aspect is to have the full history of the services so that any problem arising can be traced
back to a potential problem in the past.
Secondly, and maybe more importantly, the service record is available for every vehicle in all our workshops. This means that a truck can be serviced in any of our authorised workshops and the teams there have the full history of the truck at their fingertips.”'
There are signs on how to identify a good workshop. Using proper diagnostic tools, the health of the vehicle is then assessed. Engaging with the customer, any issue will be discussed and the best way forward. Addressing the needs of each vehicle, the team plays a crucial role: not always are the diagnostic tools able to pinpoint a problem. This is where technical understanding comes into play and the experience of staff will allow for the best way forward to be plotted. Be it a regular service or a major repair, the technicians need to be equipped with the right expertise and backed-up by a support framework that allows them to consult with the client, offering the best solution. “Again, all the details will need to be added to the system. Imagine going to a doctor where all your records are on hand so that the doctor can make the best-informed decision.”
Stressing further the importance of having the right tools, Tan reiterated that every vehicle based on their design would have their own specific tools and systems to optimize and perform the work on the trucks. Not using specialized tools for the Foton trucks may delayed the service or repair and even cause damages. Having these tools is one part of the equation, while having people trained on the correct use is the other half.
A Good Technician
Many industry players lament that finding motivated and qualified staff is difficult. Tan Chong Group looks for talent in technical schools while also maintaining their own training academy. It may help that Tan Chong Group has built a stellar reputation as a Malaysian brand of choice for consumers and employees alike.
Meanwhile, the Tan Chong Group HR department is always on the lookout for talent. Some people may be more technically inclined, thus finding a calling in a commercial vehicle workshop.
Workshop staff or technician has an important role to communicate with the driver of the vehicle when assessing the status of the truck. Almost like an involuntary technician, the driver should be able to identify any issues arising with the truck. This way, the driver and technicians are buddied-up to form a team to ensure the best possible outcome from a visit to the workshop. Driving styles impact the condition of the truck and this is where driver training, and together with telematics can work wonders to reduce maintenance cost. Again, for this to happen, the driver has to be trained, to understand the optimized way of getting the best out of the vehicle, have the right attitude. It is also important that the vehicle owner is on the same alignment on training the driver and understanding the optimized benefits.
In this respect, it is the driver that should be the first harbinger of (bad) news. Drivers need to be attuned to the way the vehicle performs, its movements, noises and reactions. Noise is generally an indication that something is not right, and drivers need to be trained to detect, process and analyse such information.
A Proper Sending Off
Once the vehicle has been serviced, there is a strict protocol regarding the final check before handing back the truck to the driver. This is to ensure that all points on the job card have been completed, completed correctly and in the prescribed manner. A short test drive will ascertain that there are no hidden issues that have been missed out. It is then recommended that the driver upon taking possession of the truck again also does a thorough inspection and a brief test drive.
In case a problem re-surfaces, it is the service record that is crucial to finding out what went wrong. There are essentially two possible root causes. First, the diagnostic has been wrong when assessing the vehicle. The other possible root cause is that the repair was not carried out correctly. In either case, retraining may have to be scheduled to prevent similar incidents from occurring. Admittedly, although the chance of something going wrong is small, however it is never zero. “Today’s work environment is a very fluid one and there is always a possibility that something goes wrong. We are only human after all, and all diagnostic is also created by humans.”
Strength in Numbers
Many transporters operate nation-wide, if not across states. With a network of 18 workshops owned by and additional authorised workshops across the country, one is never far from a AngkaTan Motor workshop where one can service a Foton. With a service and maintenance contract, the operator will have an assurance that the workshop staff is capable with the peace of mind when it comes to cost as the prices are
stipulated in the contract.
Putting all this together into a philosophy, one will notice that the approach is to maximise the lifespan of the trucks as well as the spare parts. One may be curious as to why a service provider like Angka-Tan Motor would not have an interest in selling more, thus maximizing sales and profit. The answer lies in the fact that trucks are money generating assets and thus, the less downtime, the better for the owner. “When we manage to increase uptime, then we are favoured by the clients, who would surely return to buy again, knowing that their trucks will be on the road, not in the workshop,” Tan concluded.