The Range of the Scania 45 R is Impressive: 1900 Kilometers in Three Countries
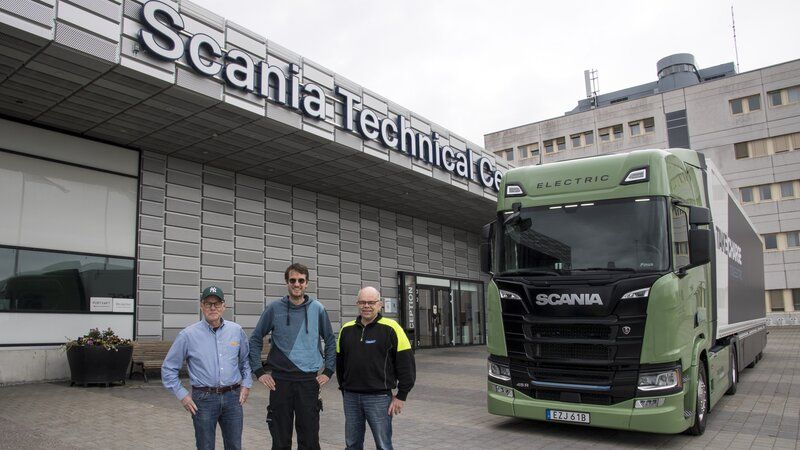
When “Trailer” drove the Scania 45 R in 1900 kilometres thorough three countries, the range and the power were impressive. This truck has the capacity for international long-distance operations already today but, the infrastructure and the charging network must improve and the prices for electricity bought along the road must come down.
By Rutger Andersson (text & photo), Stefan Boman, Martin Forsgård (photo)
How does an electrified Scania work over longer distances in long-haul operations? Me and Trailer magazine in Sweden got the question at the beginning of the year to test this together with a professional driver. In May, the time had come for me and Martin Forsgård, who runs a daily haulage operation named Bengt Forsgårds Åkeri in Habo, to set out for this exciting journey.
The unique offer was given by Örjan Åslund, responsible for press testing at Scania, but this was not about a regular press test. During one week, “Trailer” would borrow a Scania 45 R,
a tractor-and-trailer combination that belongs to Scania’s technical centre. And during this test, we were supposed to manage any potential challenges that you might face with an electric truck in international haulage on our own. The gross train weight of the combination is 32 tonnes.
The truck, that was produced in August 2023, goes under the nick-name “Pinus” which means pine forest in Latin. It has an electric machine that produces 450 kW, which corresponds with 610 hp and six battery packs that can store 624 kWh of energy in total. The so-called SOC window of the battery pack, the amount of energy that actually can be used, is set for 83 percent or 518 kWh.
Pinus everyday “keeper” is Anders Gaasedal, he has himself made a number of longer trips with Pinus, among them a trip to a test track in Germany where Pinus was used for certification tests.
Anders is an expert with great experience from the field and he has planned for a five-day round trip for us with some slack in it. And the certificate Scania provides us with is valid for some more days.
It feels safe to have Anders as a back-up and support, but the idea is that we shall manage everything on our own. After some instructions and a brief test-drive in the Södertälje area are we handed the keys, and the responsibility, for Pinus.
Day 1
The time is half past three on the Monday afternoon when we leave Scania’s technical centre and heads toward the E4 on our southbound trip.
We have plenty of energy in our batteries when we are approaching Norrköping one hour later, but we have had a piece of advice saying that Eon is operating a powerful charger there that offers 400 kW. The charging station is also said to be easy to access and one can pay with Scania’s own charging card.
Neither me, nor Martin had ever charged an electric truck on our own before. Therefore, we decide to go there and try it. It turns out not being complicated at all. After having blipped the card and put the connector in place in the CCS socket, the charging starts with a speed of 364 kw/h. The charging is very fast to begin with but when the batteries are almost full they cannot charge with the same speed.
It takes some 30 minutes to get 145 kWh. With fully charged batteries we continue on the E4 again. Since we had a slow start of the day, we decide to carry on quite late into the evening. The time is 11 AM and the trip meter says 532 kilometres when we take our daily rest in Östra Ljungby. The battery capacity we have left, 31 percent, indicates that we could have managed the whole distance without topping up in Norrköping, but for us it felt good to have some margin left.
If we had run into empty, we might have lost the trust from Scania’s side to continue with this interesting test …
While taking our rest, we use the opportunity to refill energy via the truck charging station that Börjesson Trucks operate in Östra Ljungby. The speed with the 350 kWh charger is only 179 kWh to start with. We then learned that the software is not configured in the right way. One would seldom have the need for any faster charging than what is possible if two vehicles are charging at the same time. With a check mark in the box is the top charging speed now sat on 350 kW.
Day 2
The time is 10 PM when we leave Östra Ljungby, headed to Helsingborg and the ferry that will take us to Helsingör in Denmark. After that, we will have like 200 kilometres on Själland towards Gedser and the Rostock ferry. We have been told there is a powerful charger some 10 kilometres before the harbour.
We can get eyesight of the chargers behind a McDonald’s restaurant, but it will get hard to access them without decoupling the trailer. With 61% and a remaining range of 350 kilometres we decide to skip the charging and go for a stand-by ticket for the ferry. We made it!
Something like 15 minutes before the departure time, the M/S “Copenhagen” arrives to Gedser. A large number of vehicles roll off and an equal amount of vehicles enters the ferry at furious speeds. With its electric machine is our Scania something of an outcast among its diesel siblings at lower deck. Being Swedish drivers are also rare, but we did meet a fellow Swede when having lunch.
Even though the range in “our” Pinus have offered positive surprises, we tend to agree. The charging infrastructure and competitive pricing for the electricity is not in place yet. We used part of the time on the ferry for scanning potential chargers in or around Rostock. There is no good search tool for finding all chargers suited for heavy trucks yet, but we did see an Aral filling station with a fast-charger along autobahn some 200 kilometres west of Rostock.
It is marked as a 300 kW charger, and that is correct. But the station is obviously specified for passenger cars and customers that does not have a SOC window of 518 kWh. A couple of guys in uniform that arrived in an unmarked van did approach us, but when they realised that we were actually charging they changed their minds and turned around. The price, 79 eurocent per kWh including German VAT, would not make any financial director at any haulage company happy, but we simply had to recharge new energy.
Apart from they prices, paying with normal credit cards works well. If we would have had the right apps in our cell-phones, we could most likely have had a more effortless and less expensive charging experience. As it was, we faced a “passenger car limit” of around 80 kWh/charge, which meant that we had to charge in two sessions. The speed was almost 300 kW and in the end we had to pay for 164 kWh.
This took our charging status from 51 percent to 82 percent. With a calculated range of 480 kilometres, we did continue our trip towards Kiel, Flensburg and the Danish border. The time was 11 PM when we passed Padborg. Anders Gaasedal had planned for a quite relaxed schedule were we were supposed to reach Horsens in day three, but we were approaching this stage goal already at the end of day two. We got a thumbs-up from Anders via a text with a smiley: “You keep on rolling like real international drivers”.
Although we have 14 tonnes of concrete as our “cargo” on the trailer and don’t have to do any loading or unloading, the idea is that we shall test how it works with an electric truck in international long-haul under realistic conditions.
When we stop at the truck centre in Vejle for our daily rest is the time a quarter past midnight. The trip meter says 1180 kilometres and some 32 hours have passed since we left Södertälje. Ten of these hours was spent with our first daily rest. And even though we had seen some challenges regarding the charging, we would not have been able to travel so much further with a diesel truck. Until now, most of the lost time have been more about waiting for boarding ferries than charging the truck. But the first challenge on day three is about finding a powerful charger. With 19% left we do need to charge before carrying on towards the ferry to Sweden.
Day 3
There is a fast-charger in Horsens that we are aware of, only thirty kilometres north-east of Vejle. But we decide to check if we can find a charging station near our parking place. After some searching online we find one just a kilometre away. But this one is not created for trucks either. In order not to block the entry to the charging station, Martin decouples the trailer. Then there are no problem to connect with the socket, but the communication between Pinus and the charging station does not work!
For a short moment some anxiety spreads … It is the two upper pins in the CCS connector that does the communication. I notice that one of the pins are located deeper in the connector than the other one is. When contacting Anders, he tells us that this is the way it is supposed to be, but sometimes there is a bad connection if the contact is worn. And right then we get the necessary contact.
When the charging starts, it takes approximately one hour to charge the batteries with 329 new kilowatt-hours to a SOC level of 81%. We then decide to stop the charging in order to make it to the ferry 2.40 PM from Grenå to Halmstad, Sweden. Our estimated range of 490 kilometres will be more than enough for reaching Göteborg where there are plenty of charging stations for trucks.
Our plan was to go from Fredrikshamn to Göteborg, but we could not make it to the 2 o’clock PM ferry and the next one is not leaving until 7.45 PM. And that is why we had to re-book to the “Stena Nautica” from Grenå to Halmstad, 2.10. This results in 100 kilometres less on the road in Denmark and 140 kilometres more in Sweden, what you might call “unnecessary” kilometres. This is compensated for by the fact that we will reach Göteborg earlier compared to go with the evening ferry from Fredrikshamn.
We roll off the ferry in Halmstad round 7.00 PM. After 140 kilometres on the E6 without anything noticeable, we finally reached Göteborg a couple of hours later and we continue straight from there to Alingsås for charging at Börjesson Trucks. They have a 300 kW charger where we can use our Scania card. It takes like 1:20 hours to fill the batteries with 397 kWh. When you, like in Pinus, have the SOC window set for 83 percent, the speed goes down somewhat in the end.
Day 4
By 10 AM the next day we hit the E6 again, headed for the final target, Scania Technical Centre in Södertälje. We had lunch at Rasta in Arboga and took a break in Strängnäs for teaming up with Stefan Boman, photographer that took some nice photos while we were driving during the last leg. We reached STC in Södertälje circa 4.30 PM. The battery indicator tells us that we still have 30 percent left in the batteries and a remaining range of 160 kilometres.
We could say tank you to Anders Gaasedal one day earlier than intended and hand him back the keys. He himself have, as a vital part of Scania’s development process, made a number of longer trips with this very truck. We could now recognise a lot of the experiences he presented for us before we left. During our roundtrip we hade a Krone trailer with some aerodynamical improvements behind our truck. The tractor had the IVD bumper extension that is allowed in order to reduce air drag and the side skirts were also extended in order to optimise the airflow between the tractor and the trailer.
These aerodynamical improvements will of course increase the range and have a positive effect on the energy consumption, but they are signs of the time we live in. Since the electric machine has such a high degree of efficiency and very small losses, will the aerodynamics become even more important for electric long-haul vehicles.
During this test, the Scania had an energy consumption and a range that was a positive surprise for us. When you look upon the electricity we charged during this long trip, the average consumption was 9,2 kWh per 10 kilometer. This equals the energy content from less than one litre of diesel!
The electric machine is situated right behind the cab, it has three electric motors with a total output of 450 kW and a six-speed gearbox. Due to the fact that it has two outgoing axles, there is no interruption in the power delivery when changing gears. And we really had to pay attention when trying to identify when the gearbox was shifting between the five first gears. Gear number five is a direct gear, which is considered as the most favourable one from an economic perspective when cruising at normal speed.
With a total gross train weight of 32 tonnes, the truck is very powerful, it seldom had to shift down when going uphill. We cannot remember any single uphill where the truck went under the set speed of 80 to 85 km/h voluntarily, but sometimes will the cruise control with active prediction reduce the speed in order to use the kinetic energy for rolling over crests.
When rolling out downhill, the energy consumption is zero. When reaching the set top speed, which varied from +2 to +6 km/h, in steeper downhills it recuperated energy when the electric machine doubled as a powerful retarder which has an output of up to 600 kW.
The electric machine has a very flat torque curve, which contributes to the very few gear changes. Pinus is also equipped with Scania’s EAS-system for electric steering, a climate package, premium seats and air suspension on both axles.
The combination felt very stable on the road and the overall drivability was very good. Also the comfort was good and not even our longer stints behind the wheel felt tiring. Whether the silent electric machine contributed to this feeling or not is hard to say. Also regular diesel trucks offer high driver comfort nowadays.
Our test vehicle offers a lot of different settings but the ones we used during our trip felt meaningful. We oversaw speed, the energyconsumption/recuperation in real time, the total consumption, the average consumption since start, SOC status, the estimated range and the energy that was used when charging for cooling the batteries.
Compared to what one is used with is the tacho missing, but the flat torque curve makes it irrelevant when driving an electric truck. It is obvious that 1900 kilometres trip with the Scania 45 R “Pinus” was a different. pleasant and nice week that offered many learnings. One conclusion is that these trucks are in the frontline in today’s electrical race. But there are challenges that must be solved when it comes to aspects such as infrastructure and prices for electricity before electric trucks will become a frequent choice for international long-haul.
Facts:
Scania 45 R 4x2
Powertrain: EM C3-6 electric machine 450 kW (610 hp) with an integrated gearbox with six speeds
Batteries: 624 kWh (6x106 kWh), SOC window (usable energy) 83%/518 kWh
Front axle: air suspension, 9 000 kilo
Rear axle: air suspension, 11500 kilo, R756, gearing 1:3.36
Wheel base: 4150 mm
Dimensions: length 6450 mm, width 2550 mm, height 4000 mm
Service weight, truck: 11 110 kg, trailer: 7.400.
Current train weight: 32 100 kg.
Facts about charging and energy consumption
When we reached our target in Södertälje- the truck have had an average consumption of 9.06 kWh/10 kilometres according to the onboard computer. During our 1902.5 kilometres we consumed 1723.4 kWh.
It is not science, but the correlation with the energy we charged the truck with is good. Day 1 we charged the batteries in Norrköping. When we arrived to Alingsås in the evening of day 3 we had travelled 1360 kilometres more. When we had filled the batteries in Alingsås had we spent 1255 kWh for that distance. That corresponds with an average consumption of 9.2 kWh/10 kilometres. This consumption includes the energy losses we had when the truck was not rolling, and among other things cooling the batteries when charging. We handed back the test vehicle with a remaining battery capacity of 30 percent.
The average consumption, according to the onboard computer, would most likely have risen somewhat if we had charged it to 100 percent of the SOC window. Scania 45 R has six batteries with 624 kWh in total. The owner can chose to set the SOC window to 75 percent or 83 percent.
This gives a usable energy of 518 or 468 kWh. Choosing the lower level will of course have a negative impact on the range, but from a battery perspective is the lower level better since they are doing well with slow charging and not going all the way to full. When the SOC window is set to 83 percent and almost full, the charging speed goes down and a reflection we made is that the losses from cooling the batteries when charging become higher per kWh.
“The charging infrastructure and the price for electricity is decisive”
Martin Forsgård owns and runs Bengt Forsgård Åkeri and has a huge interest in heavy trucks, all the way from yesterday’s premium trucks to new technology. His fleet consists of 15 modern bulk carriers that are in daily use. Scania R 590 is the dominating truck.
“My experience is that the V8s suit us well and does a great job in the kind of operation that we have”, says Martin Forsgård.
In the more hobby-related part of his fleet can, among other things, a replica of his fathers first new truck be found, a renovated Scania LBS 140 Super from 1974. While having a huge interest on trucks from the good old days, Martin is also keen about being in the frontline regarding technological developments. During our 1900 kilometres trip we were surprised over the range that “our” Scania 45 R could offer. Our GTW, 32.1 tonnes, is considered to be the average weight for five-axle combinations in international operations on European highways.
“It would have been exciting to test a 45 R as a 64-tonnes combination. It might work on the reoccurring transports we are doing. We could the charge the batteries over-night and recharge at the customer”, says Martin Forsgård. Charging opportunities along the route while having the daily rest would also increase the opportunities: “We would not necessarily need to have access to 350 – 400 kW. If the batteries are fully charged when it is time to depart would be enough”.
Martin says that his company would be glad to take part in field tests and such with electric trucks, but becoming a realistic alternative must the total cost of ownership compared to a conventional truck come down for electrified trucks. “What is the cost an how much are the customer willing to pay? If the cost is higher compared to a conventional truck must the customer be onboard as well. And the infrastructure and the electricity prices you have to pay along the route is also essential”.